旭化成のサステイナブルな繊維「ベンベルグ」
みなさんは、旭化成の「ベンベルグ」という素材についてご存知でしょうか。素材自体がサステイナブルであることはもちろんですが、原料調達から最終製品までのバリューチェーン全体を持続可能なビジネスモデルとして構成する努力が続けられています。
2021年6月24日付け日経ESG電子版に掲載された記事より、
“サステイナブルな繊維として注目されている素材がある。総合科学メーカーの旭化成が製造する化学繊維のキュプラ「ベンベルグ」だ。なめらかな肌触りで独特の光沢と風合いがあり、様々なファッション製品や衣類の裏地などに使われている。旭化成は1928年、独ベンベルグ社が開発した技術を導入し、1931年に宮崎県延岡市に工場を建設して操業を開始した。現在、世界で唯一、キュプラを生産するメーカーだ。”
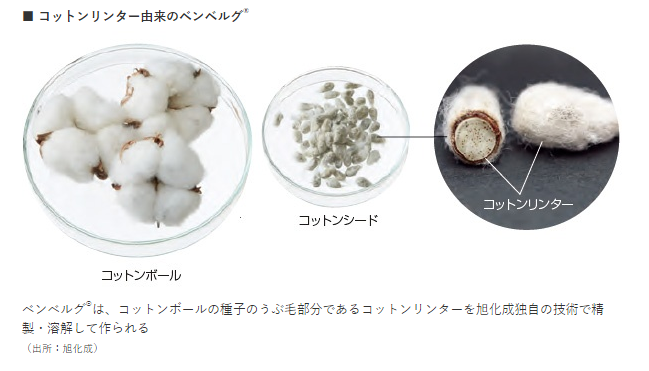
”世界の繊維生産量の0.02%と極めてニッチな製品のベンベルグは、綿糸の原料となるコットンボールの種子のうぶ毛部分、コットンリンターを原料とする。コットンリンターは綿実油を圧搾する際の副産物で、綿糸としては使われない。旭化成はその未利用繊維を独自の技術で精製・溶解して再生繊維に仕上げている。天然由来のベンベルグは環境負荷が少ない。生分解性を備え、夏の条件下(温度35度、湿度80%)で土に埋めると約2ヶ月で生地の重量が半分以下になる。繊維を燃やしても有害物質がほとんど発生しない。”
”旭化成は、同じくコットンリンターを原料としたキュプラ長繊維不織布「ベンリーゼ」も生産している。ベンリーゼは吸液性と保液性が高く、毛羽立ちが少ないという特徴がある。接着剤を用いず、繊維の自己接着力を利用して作られるので、不純物が少ない。1974年の生産開始以来、産業用(ワイパー)や美容用(フェイスマスク)、コロナ禍においては特に医療用で販売が拡大し、この10年で売り上げは約3割伸びた。“
”ベンベルグとベンリーゼは生産体制の面でも持続可能性が高いと言える。自社発電設備として水力発電設備9基、バイオマス発電設備2基を備えていることだ。延岡地区の工場が使用する電力の33%を水力で、6%をバイオマスで賄っており、再生可能エネルギー比率は約4割に上る。生産過程で出た繊維くずはバイオマス発電の燃料として再利用するなどリサイクルも徹底しており、99.8%のゼロエミッション化を達成している。こうした環境下で生み出されるベンベルグとベンリーゼは、国際的な認証「GRS(Global Recycled Standard)」、繊維製品の安心・安全を証明する「エコテックス規格100」なども取得している。”
”旭化成は、サステイナブル素材のベンベルグを通じてCSV(共有価値の創造)ビジネスにも力を注ぐ。
CSV(共有価値の創造、Creating Shared Value):企業における経済的な価値創出だけでなく、社会と共有の価値を想像していくことが目指される。
その舞台はインド。ベンベルグは民族衣装のサリーやデュパタ(大判のストール)の素材として40年以上にわたって親しまれ、現在は年間4000~5000トンの原糸を輸出する最大市場だ。旭化成は2016年から、SDGs達成に向けて国連開発計画(UNDP)が主導する「ビジネス行動要請(BCtA)」に参加している。原料調達から最終製品まで、バリューチェーンのすべての段階における技術指導や雇用創出、安定収入の確保などの課題解決に取り組んでいる。”
”具体的な活動として、原材料メーカーに対して、2009年からコットンリンターを採取するためのデリンティング設備や分析機器を無償で貸与してきた。旭化成の技術者が品質や効率向上の指導も行っている。ベンベルグ原糸を販売する生地工場(約40社)に対しては、染色工程でのスレ・シワの抑制方法や時間・湿度の設定など、工業的な生産管理の技術・ノウハウを供与している。”
”旭化成の技術指導により品質が安定したため、ベンベルグ素材の民族衣装の需要は拡大している。技術指導を始めた2000年以降、現地のベンベルグ生地生産者による販売量は約6倍に増加した。また、インドの原料メーカーからのコットンリンターの購入量は設備無償貸与を開始した2010年から2019年の間で3倍に増加し、これらの活動が現地の雇用拡大や収入増につながった。インドの繊維産業やファッション業界の未来を担う学生向けの教育支援活動にも取り組んでいる。デザインや服飾分野の大学と連携し、衣服の素材やベンベルグについての講義や、ファッションショーへの作品の素材提供などを行っている。”